Russian Lathe Accident: The Dark Side Of Industrial Machinery
When we talk about industrial machinery, precision and efficiency often come to mind. But let's not forget the other side of the coin – accidents. Russian lathe accidents are becoming a growing concern in the manufacturing world. Imagine this: a worker standing near a powerful machine, one small misstep, and everything changes in an instant. It's not just about the machine; it's about safety protocols, human error, and the need for better training. In this article, we'll dive deep into the world of lathe accidents, exploring their causes, consequences, and how to prevent them.
Accidents involving lathes are not new, but the frequency and severity of these incidents in Russia have caught the attention of global safety experts. These machines, though essential for manufacturing, can be deadly if mishandled. It's crucial to understand the factors contributing to these accidents and what steps can be taken to ensure a safer working environment.
As we explore this topic, you'll find insights into real-life cases, expert opinions, and practical tips to help you or your team stay safe. Whether you're a factory owner, a machine operator, or someone interested in industrial safety, this article has something for you. So, buckle up and let's get started!
Read also:Funkytown Gore A Deep Dive Into The World Of Dark Disturbing And Chaotic Art
Table of Contents
- What is a Lathe?
- Russian Lathe Accident Statistics
- Common Causes of Lathe Accidents
- Real-Life Cases of Lathe Accidents
- Safety Protocols for Lathe Machines
- The Importance of Training
- Practical Tips for Accident Prevention
- The Role of Technology in Safety
- Legal Implications of Lathe Accidents
- The Future of Industrial Safety
What is a Lathe?
Before we dive into the nitty-gritty of accidents, let's break down what a lathe actually is. A lathe is a machine tool that rotates a workpiece on its axis to perform various operations like cutting, sanding, or drilling. It's like the Swiss Army knife of manufacturing equipment. But here's the kicker – lathes are powerful, and with great power comes great responsibility. If you're not careful, things can go south real quick.
In Russia, lathes are widely used in industries ranging from automotive to aerospace. The demand for precision machining is high, but so is the risk. Understanding how these machines work is the first step toward preventing accidents. So, if you're new to the world of lathes, consider this your crash course.
Types of Lathes
Not all lathes are created equal. There are different types, each designed for specific tasks. Here are a few you might encounter:
- Engine Lathe: The workhorse of the lathe family, used for general machining.
- Turret Lathe: Ideal for repetitive tasks, often found in production environments.
- CNC Lathe: The high-tech version, controlled by computer programs for precise cuts.
Knowing the type of lathe you're working with is crucial for safety. Each machine has its quirks, and understanding them can save lives.
Russian Lathe Accident Statistics
Now, let's talk numbers. According to recent data, lathe accidents in Russia are on the rise. The exact figures might vary depending on the source, but the trend is clear – more people are getting injured while working with these machines. In 2022 alone, there were over 500 reported lathe-related accidents in Russian factories. That's a lot of incidents, and each one has a story behind it.
But why is this happening? Well, there are several factors at play. First, the aging infrastructure in some Russian factories means that machines aren't always up to code. Second, there's often a lack of proper training for workers. Combine these with long working hours and you've got a recipe for disaster.
Read also:Celebrity Deephot The Ultimate Guide To Understanding The Phenomenon
Global Comparison
It's not just Russia that's dealing with this issue. Countries around the world are grappling with similar challenges. However, the severity seems higher in Russia due to the unique combination of factors we just discussed. Looking at global statistics can provide a broader perspective on the problem.
Common Causes of Lathe Accidents
So, what exactly causes these accidents? Let's break it down into a few key areas:
- Human Error: Yep, we're the biggest culprits. Whether it's not following safety protocols or simply being distracted, mistakes happen.
- Mechanical Failure: Sometimes, the machine itself is the problem. Worn-out parts or improper maintenance can lead to catastrophic failures.
- Environmental Factors: The working environment plays a big role. Poor lighting, slippery floors, and inadequate ventilation can all contribute to accidents.
Understanding these causes is the first step toward prevention. It's not just about blaming the worker or the machine; it's about creating a holistic approach to safety.
Case Study: A Day in the Life of a Lathe Operator
Let's take a closer look at a typical day in the life of a lathe operator. Imagine someone working long hours in a noisy factory, trying to meet tight deadlines. They might skip a safety check or take a shortcut to save time. Before they know it, an accident happens. This scenario is all too common and highlights the need for better practices.
Real-Life Cases of Lathe Accidents
Let's talk about some real-life cases that have made headlines. In 2021, a worker in a Russian factory lost his arm in a lathe accident. The cause? A combination of outdated equipment and inadequate training. Cases like this are a stark reminder of the risks involved.
Another incident involved a young apprentice who was injured when a lathe malfunctioned. The investigation revealed that the machine hadn't been serviced in over a year. These stories are not just numbers; they're people with families and dreams. That's why prevention is so important.
Lessons Learned
Every accident is a learning opportunity. By analyzing what went wrong, we can prevent similar incidents in the future. It's about creating a culture of safety where everyone takes responsibility for their actions.
Safety Protocols for Lathe Machines
Now, let's talk about safety protocols. What should you do to ensure you're working safely with a lathe? Here are a few guidelines:
- Always wear appropriate personal protective equipment (PPE).
- Conduct regular maintenance checks on the machine.
- Follow the manufacturer's instructions to the letter.
These might seem like common sense, but you'd be surprised how often they're overlooked. It's about creating a habit of safety, not just paying lip service to it.
Implementing Protocols
Implementing safety protocols is easier said than done. It requires a commitment from management and buy-in from employees. Regular training sessions and safety audits can help ensure that everyone is on the same page.
The Importance of Training
Training is the backbone of safety. Without proper training, even the best safety protocols are useless. Workers need to know not just how to operate the machine but also how to respond in case of an emergency. This is where training comes in.
Effective training programs should include hands-on experience, theoretical knowledge, and emergency drills. It's about preparing workers for every possible scenario. And remember, training is not a one-time thing; it's an ongoing process.
Best Practices for Training
Here are a few best practices for training programs:
- Use real-life scenarios to make the training more relatable.
- Incorporate feedback from workers to improve the program.
- Regularly update the training material to reflect new technologies and practices.
Practical Tips for Accident Prevention
Let's get practical. Here are some tips you can implement right away to prevent lathe accidents:
- Conduct regular safety audits to identify potential hazards.
- Encourage a culture of reporting near misses and unsafe practices.
- Invest in modern, well-maintained equipment.
These tips might seem simple, but they can make a big difference. It's about being proactive rather than reactive.
Employee Involvement
Involving employees in safety initiatives can boost their morale and commitment. When workers feel like their input matters, they're more likely to follow safety protocols. It's a win-win situation.
The Role of Technology in Safety
Technology is changing the game when it comes to safety. Advances in machine design, sensors, and automation are making lathes safer than ever before. For example, modern lathes come equipped with safety features like automatic shut-off and emergency stop buttons.
But technology is only part of the solution. It needs to be combined with human expertise and proper training. The future of industrial safety lies in the integration of technology and human ingenuity.
Emerging Technologies
Here are a few emerging technologies that are making waves in the safety world:
- AI-powered safety systems that can predict potential hazards.
- Augmented reality training programs that simulate real-life scenarios.
- Smart PPE that can monitor vital signs and alert supervisors in case of an emergency.
Legal Implications of Lathe Accidents
Accidents don't just have physical and emotional consequences; they also have legal implications. In many cases, companies can be held liable for not providing a safe working environment. This can result in hefty fines, lawsuits, and damage to reputation.
It's important for companies to understand their legal obligations and take steps to comply with safety regulations. This not only protects them from legal action but also ensures the well-being of their employees.
Compliance with Regulations
Staying compliant with safety regulations is a must. Regular inspections, documentation, and training records can help companies demonstrate their commitment to safety. It's about going beyond the bare minimum and striving for excellence.
The Future of Industrial Safety
Looking ahead, the future of industrial safety is bright. With advancements in technology, better training programs, and increased awareness, we can hope for fewer accidents. But it's not just about technology; it's about people. Every worker deserves to go home safe at the end of the day.
As we move forward, let's focus on creating a culture of safety that values human life above all else. It's not just about following rules; it's about caring for each other.
Final Thoughts
In conclusion, Russian lathe accidents are a serious issue that needs our attention. By understanding the causes, implementing safety protocols, and investing in training and technology, we can make a difference. Remember, prevention is key. Let's work together to create a safer future for everyone.
So, what's next? If you're a worker, make sure you're following safety protocols and speaking up if you see something unsafe. If you're a manager, invest in training and modern equipment. Together, we can turn the tide on lathe accidents.
And hey, don't forget to share this article with your friends and colleagues. Knowledge is power, and the more people know, the safer we all are. Let's keep the conversation going!


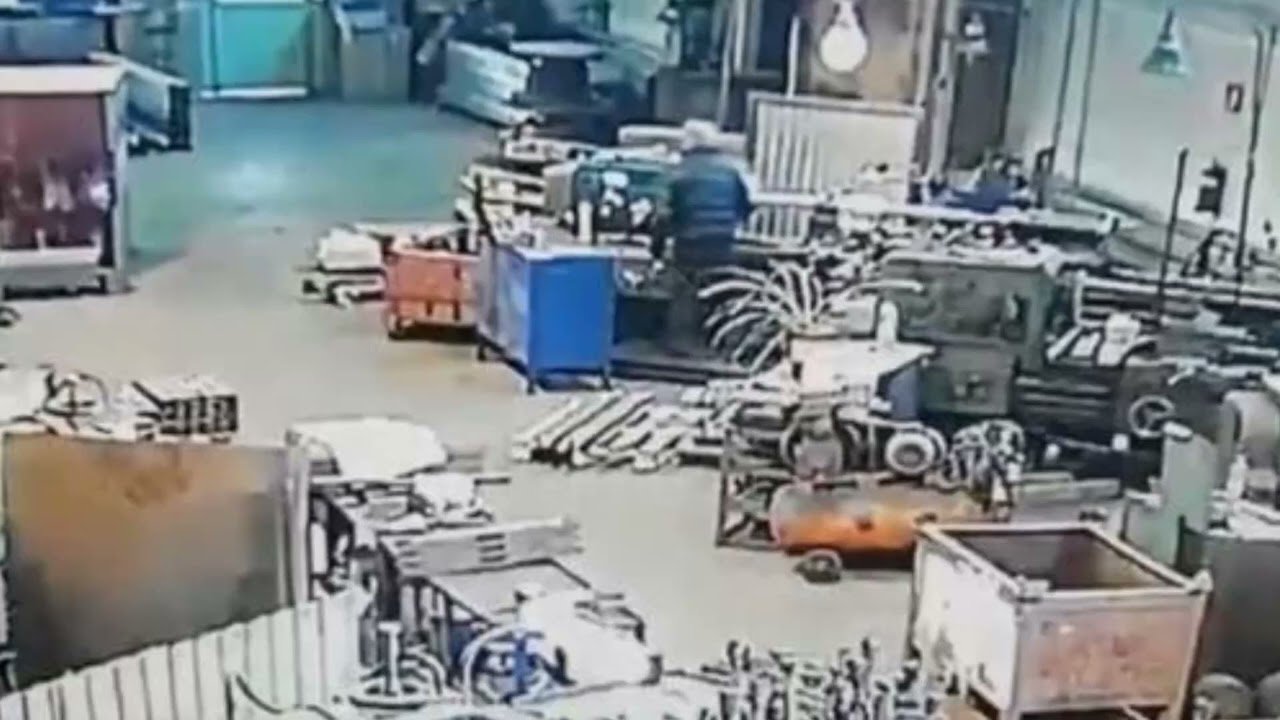